Types of Secondary Manufacturing Processes
Understanding the different types of secondary manufacturing processes available is key to ensuring your parts meet the performance, aesthetic, and durability requirements
Primary vs Secondary processes
In manufacturing, creating a finished part often involves distinct stages. Primary manufacturing processes are the foundational steps where the main shape of the component is created, typically through material removal like CNC milling or turning. Think of this as establishing the part's core geometry. Secondary processes are the operations performed after the primary machining is complete. These refine the part, enhance its properties, or add specific features – including treatments like heat treating or powder coating, finishing steps like deburring, or functional additions like engraving or assembly. Essentially, primary processes build the structure, while secondary processes add the necessary finish, protection, and final details to the parts.
Category 1. Surface treatments & coatings
Many components require specific surface treatments or coatings to meet performance, durability, or aesthetic requirements. These secondary processes enhance the part's properties and ensure it functions reliably in its final application. Spex offers several key surface treatment options, managed seamlessly within your production workflow to simplify your supply chain.
Anodizing
Anodizing is an electrochemical process
specifically for aluminum (and sometimes titanium) that grows a controlled oxide layer directly from the base material. This isn't a coating applied on top; it's an integral conversion of the surface itself. The part acts as the anode in an electrolytic cell, typically an acid bath, resulting in a hard, porous layer. Common types include Type II (using sulfuric acid, offering good corrosion resistance and dyeability) and Type III "Hardcoat" (often using lower temperatures/different parameters for a much thicker, harder, more wear-resistant layer).
Key Benefits:
Enhanced Corrosion Resistance: Significantly increases protection against environmental factors and oxidation.
Improved Wear Resistance: Creates a harder surface (especially Type III) suitable for components subject to friction, sliding, or abrasion.
Aesthetic Options: The porous nature allows for dyeing in various colors before sealing, ideal for branding, identification, or appearance.
Non-Conductive Surface: The resulting aluminum oxide layer provides electrical insulation.
Electroplating
Electroplating uses an electric current to deposit a thin layer of a desired metal (like nickel, zinc, chromium, tin, copper, silver, or gold) onto the surface of a conductive part (the cathode) from a solution containing ions of the plating metal (the electrolyte). This process modifies the surface properties to add characteristics the base material lacks. The choice of plating material depends heavily on the intended application.
Key Benefits:
Corrosion Protection: Zinc and nickel plating are common choices for protecting steel from rust.
Enhanced Wear Resistance: Hard chrome plating significantly increases surface hardness and lubricity.
Improved Conductivity: Copper, silver, and gold plating are used to enhance electrical conductivity for connectors and contacts.
Solderability: Tin plating improves the ability to solder components.
Aesthetic Appeal: Provides finishes like bright chrome, brushed nickel, or the appearance of precious metals.
Powder Coating
Powder coating involves spraying a fine, dry powder (typically a thermoset or thermoplastic polymer) onto a grounded metal part using an electrostatic charge. The charged powder adheres to the part, which is then heated in an oven. This curing process melts the powder, causing it to flow together and chemically cross-link, forming a uniform, durable, high-quality finish. It's known for being tougher and more impact-resistant than conventional liquid paints.
Key Benefits:
High Durability: Creates a thick, robust coating highly resistant to chipping, scratching, chemicals, and fading.
Excellent Corrosion Resistance: Forms a strong barrier against moisture and environmental elements.
Wide Range of Colors & Textures: Offers extensive aesthetic options, including various gloss levels, textures (smooth, wrinkled, matte), and custom colors.
Environmentally Friendlier: Generally produces fewer volatile organic compounds (VOCs) compared to liquid painting processes.
Heat Treating
Heat treating refers to a process involving heating and cooling metals to intentionally alter their internal microstructure. This modification changes the material's physical and mechanical properties without changing the part's shape. Common processes include Annealing (softening metal, improving machinability, relieving stress), Hardening (heating and rapidly quenching to increase hardness and strength), Tempering (reducing brittleness and improving toughness after hardening), and Stress Relieving (reducing internal stresses caused by machining or welding). The specific temperatures, times, and cooling rates are critical for achieving the desired outcome.
Key Benefits:
Increased Hardness & Strength: Crucial for components needing high wear resistance or load-bearing capacity.
Improved Durability & Toughness: Tailors the material's ability to withstand impact and deformation.
Enhanced Machinability or Formability: Annealing can make materials easier to work with in subsequent steps.
Dimensional Stability: Stress relieving helps prevent warping or distortion over time or during later processes.
Category 2. Part Marking & Identification
This secondary process enables traceability, branding, or conveying critical information directly on a component often requires precise marking. This adds permanent identification or logos after the primary machining is complete. Spex offers different methods to suit various material types, durability requirements, and aesthetic needs.
Laser engraving
Laser engraving utilizes a highly focused beam of light to precisely remove or alter the surface material of a part, creating permanent marks. The laser's energy vaporizes or melts the material in a controlled manner, resulting in high-contrast, high-resolution markings without direct contact with the part. This method is known for its speed, precision, and versatility across various materials, including metals, coated metals, and some plastics.
Key Benefits:
High Precision & Detail: Capable of creating very fine lines, small text, complex logos, barcodes, and QR codes accurately.
Permanent Marking: The mark is etched into the material, providing excellent durability for identification and traceability (part numbers, serial numbers, lot codes).
Non-Contact Process: Minimizes the risk of part distortion or damage, suitable for delicate components.
Speed & Efficiency: Generally a fast process, well-suited for high-volume marking requirements.
CNC engraving
CNC engraving employs a rotating cutting tool, similar to those used in milling, guided by a CNC program to physically carve or cut marks into the part's surface. Unlike laser engraving, this method removes material mechanically, creating marks with tangible depth. This inherent depth makes CNC engraving extremely durable and suitable for parts exposed to harsh environments, abrasion, or subsequent painting/coating processes where the mark needs to remain visible.
Key Benefits:
Exceptional Durability: Creates deep, physical marks that resist wear, abrasion, and environmental exposure.
Clear Depth: The physical indentation provides clear visibility, even if the surface is later painted or coated.
Suitable for Tough Conditions: Ideal for industrial components where markings must withstand significant handling or harsh operating environments.
Distinct Aesthetic: Offers a classic, traditional engraved look with tangible depth.
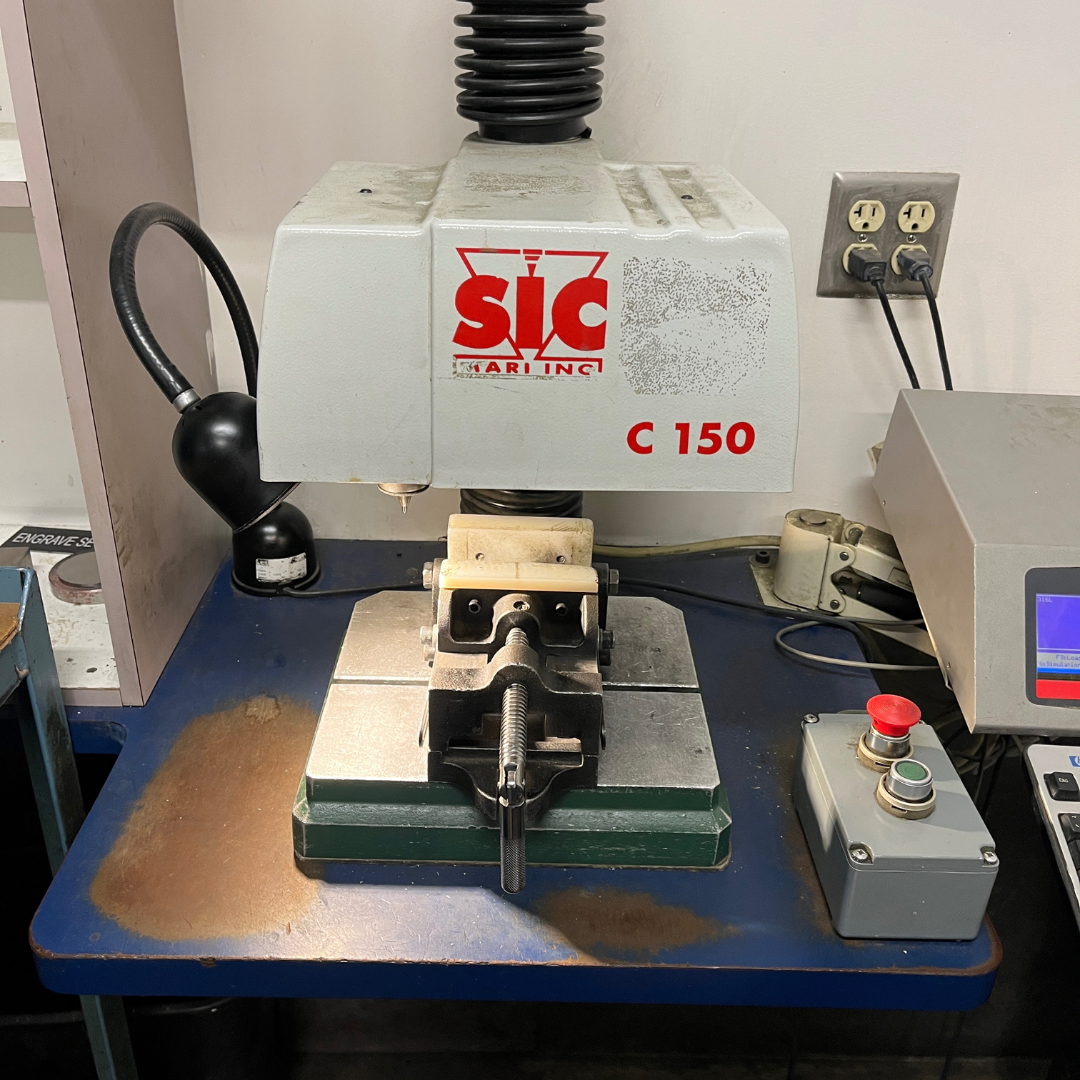
Category 3. Finishing & Refinement
Even the most precise machining operations can leave behind small imperfections like sharp edges or burrs – tiny ridges or protrusions of material. Finishing and refinement processes address these details, ensuring parts are not only dimensionally accurate but also safe to handle, functionally sound, and aesthetically complete.
Deburring & Edge Finishing
Deburring is one of the most common and critical secondary operations, focused entirely on removing the unwanted burrs and sharp edges left behind by cutting tools during machining. These seemingly minor imperfections can cause major problems: they can pose safety hazards during handling and assembly, interfere with the proper fit or function of mating parts (especially for sealing surfaces), and potentially break off later, creating foreign object debris (FOD) in critical systems. The deburring process smooths these rough areas using various techniques appropriate for the part's geometry, material, and tolerance requirements – methods can range from careful manual finishing with specialized tools to automated processes like tumbling (using abrasive media in a rotating barrel) or brushing.
Key Benefits:
Improved Safety: Eliminates sharp edges, making parts safe for handling and assembly personnel.
Ensured Proper Function: Guarantees parts fit together correctly, prevents interference, and allows for effective sealing where required.
Enhanced Reliability: Reduces the risk of burrs breaking off and causing contamination or damage during operation.
Consistent Quality & Appearance: Provides a clean, finished look and feel to the component.
Category 4. Assembly & Sub-Assembly
For many applications, a precision machined component is just one part of a larger system. Streamlining your production often means receiving more than just individual pieces. Assembly and integration services bridge the gap between component manufacturing and your final product, simplifying your workflow significantly.
Assembly & Sub-Assembly
This secondary process involves taking Spex-manufactured precision components and joining them with other items – such as standard hardware (screws, nuts, bolts), specialized fasteners, seals (like O-rings), brackets, or even other customer-supplied parts – to create a more complete unit or sub-assembly. Instead of receiving individual parts that require further handling and assembly steps at your facility, you receive integrated units ready for the next stage of your production or final assembly line. This service moves beyond component supply to providing a more holistic manufacturing solution.
Key Benefits:
Streamlined Production Flow: Reduces the number of steps and handling required at your facility, freeing up your internal resources.
Reduced Vendor Management: Consolidates component manufacturing and assembly with a single, reliable partner, simplifying procurement and logistics.
Ensured Proper Fit & Function: Allows potential integration issues to be identified and resolved by the component manufacturer, ensuring parts work together as intended.
Simplified Inventory & Logistics: Manage fewer individual SKUs by receiving pre-assembled units.
Faster Time-to-Market: By handling assembly steps, Spex can help shorten your overall production cycle.